No me gusta la frase “La historia se repite”, pero en este caso, creo que ocurrirá.
No es la primera vez del amoníaco en el canal, os dejo los link a dos análisis imperdibles para conocer a fondo la tecnología a 83) Historia y química detrás de la síntesis del producto que ha ayudado a alimentar el planeta: Amoníaco (I) y a 84) Descarbonización: Fertilizantes sostenibles gracias al hidrógeno verde. Ya por eso solo, merece la suscripción de pago al canal.
El método de síntesis de amoníaco fue inventado por Fritz Haber y Robert Le Rossignol en 1909, y fue ampliado por Carl Bosch y sus colegas de la firma alemana BASF, que abrió la primera planta comercial en 1913 en Oppau, cerca de su fábrica de Ludwigshafen. Para fabricar ese amoníaco, el hidrógeno se produjo a partir de un proceso basado en carbón.
Sin embargo, hace algo más de 100 años, concretamente en 1921, el químico italiano Luigi Casale introdujo el primer rival comercial viable de lo que se conoció como el proceso Haber-Bosch. Su proceso de amoníaco sintético se basó originalmente en hidrógeno generado por la electrólisis del agua. La tecnología de síntesis de amoníaco de Casale se convirtió en la clave para la globalización de la industria del amoníaco sintético.
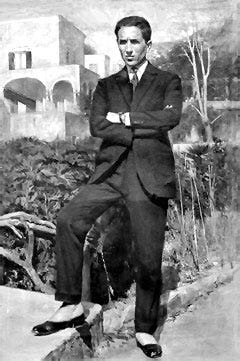
Actualmente, se producen alrededor de 183 Mt de amoníaco al año, casi exclusivamente a partir de materias primas fósiles, principalmente gas natural y carbón. La producción renovable de amoníaco representa hoy solo el 0,01% de la producción mundial.
Pero como podéis observar en el siguiente gráfico hace 100 años el hidrógeno renovable copaba el 30% del mercado de la materia prima para el amoníaco. Aunque, obviamente, el mercado no tenia la envergadura que tiene hoy en día.
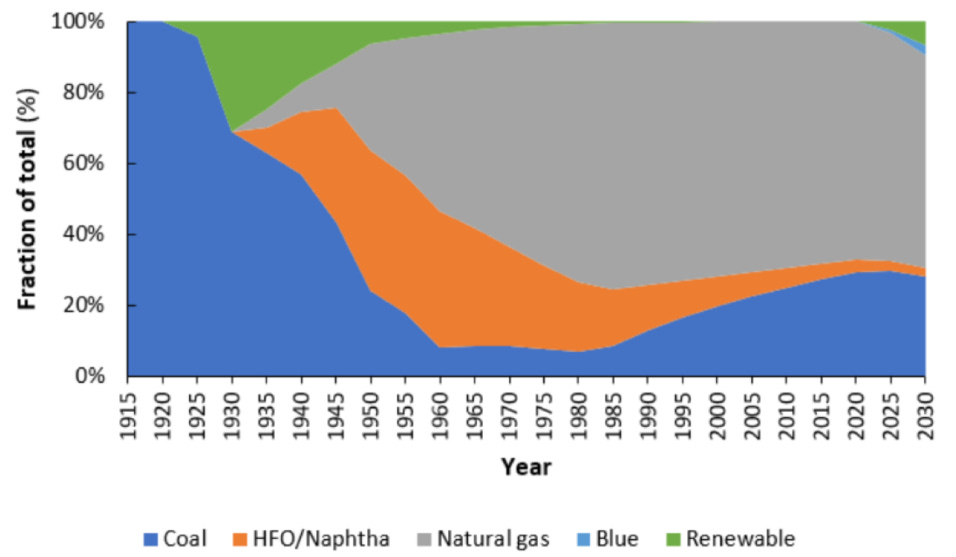
En la figura se muestra una descripción esquemática de la síntesis de amoníaco basada en electrólisis durante la década de 1920. En ese momento, la síntesis de amoníaco basada en electrólisis era la tecnología con el menor consumo de energía para la síntesis de amoníaco, aproximadamente 48–50 GJ/Tn NH₃, y mucho menor que la síntesis de amoníaco basada en carbón, aproximadamente 95–100 GJ/Tn NH₃.
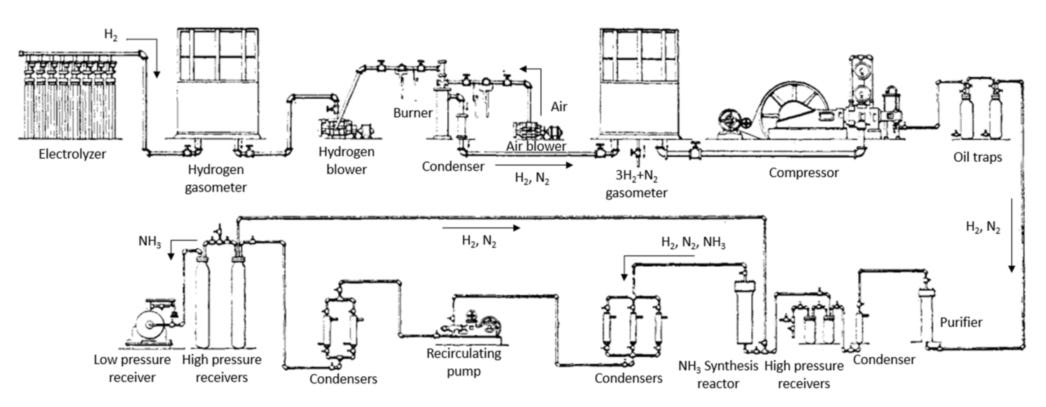
Pero Ager, ¿Cómo siendo más eficiente no cuajó a largo plazo?
La eficiencia no lo era todo en aquel entonces, ya que, el carbón y el coque estaban disponibles a bajo costo en varios países, por ejemplo en Alemania, Bélgica, Francia, los Países Bajos y el Reino Unido, lo que hacía que la producción de amoníaco de origen fósil en estos países fuera más económica que la producción de amoníaco renovable.
El hidrógeno renovable se producía principalmente mediante la división del agua, es decir, la electrólisis. Las centrales hidroeléctricas se combinaron con electrolizadores alcalinos para producir hidrógeno puro. Obviamente, no existían las tecnologías PEM ni AEM.
Los electrolizadores de la década de 1920 consumían normalmente alrededor de 5,2 kWh/Nm³ H₂.
Desde entonces, los electrolizadores se han optimizado para alcanzar un consumo de energía de aproximadamente 4,2 a 4,7 kWh/Nm³ H₂.
En los procesos renovables, el nitrógeno se obtenía del aire mediante destilación criogénica, o eliminando el oxígeno quemando parte del hidrógeno con aire para producir agua, que posteriormente se eliminaba por condensación. Esta última tecnología sólo fue económica en operaciones a pequeña escala (<5 Tn NH₃/día). La producción de nitrógeno mediante separación criogénica de aire es la tecnología preferida para la síntesis de amoníaco basada en electrólisis a gran escala.
Aunque en 1920 la electricidad era más costosa que el carbón como fuente de energía, en plantas pequeñas la producción de amoníaco renovable fue competitiva. Sin embargo, la economía de escala hizo que plantas grandes como IG Farben, ICI, Du Pont y Allied Chemical fueran desplazando del mercado al amoniaco renovable.
Sin embargo, debido a que el consumo de energía de la síntesis de amoníaco basada en carbón, y especialmente de la síntesis de amoníaco basada en gas natural, disminuyó después de mediados de la década de 1940, la producción de amoníaco basada en electrólisis se volvió menos competitiva.
Este fue el caso, en particular, a partir de mediados de la década de 1960, tras la introducción de las novedosas unidades de ahorro de energía de alta capacidad y de tren único por parte del contratista de ingeniería M.W. Kellogg.
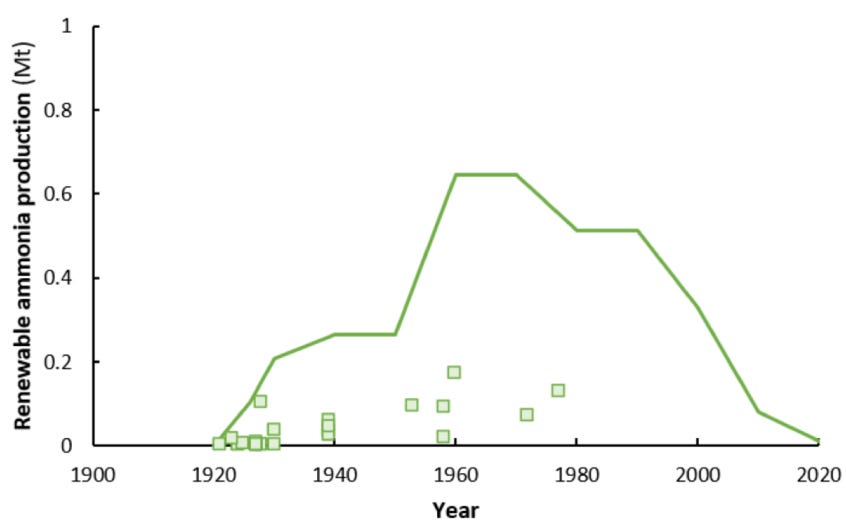
Durante la década de 1920, se fabricó amoníaco renovable para proporcionar seguridad alimentaria nacional, especialmente en Italia y Japón. El amoníaco y los fertilizantes derivados se convirtieron cada vez más en productos básicos globales en las décadas siguientes.
En 2020, de las 185 MT de amoníaco producidas, el 72 % dependió del reformado con vapor a base de gas natural (SMR), el 26 % de la gasificación del carbón, alrededor del 1 % de los productos derivados del petróleo y una fracción de punto porcentual de la electrólisis. Mediante el reformado con vapor a base de gas natural (SMR) se emiten 1,8 T CO₂/ T NH₃, y mediante la gasificación del carbón, 3,2 T CO₂/ T NH₃.
Los factores clave para el renacimiento de la producción renovable de amoníaco incluyen:
Aumento de las multas por emisiones de carbono.
Disminución del costo de la electricidad renovable proveniente de la energía solar y eólica.
Disminución del costo de los electrolizadores y/o el aumento de la capacidad de los electrolizadores.
Desarrollo de nuevas tecnologías de electrólisis que permitan la producción de hidrógeno más competitivo, como por ejemplo, tecnología aniónica.
En resumen, el amoníaco es una pieza fundamental para nuestra sociedad. Proyectos empresariales que pretendan descarbonizar tanto el hidrógeno como el amoníaco son necesarios, ya que, la sociedad de siglo XXI está concienciada con la sostenibilidad, y necesita pequeños pasos para avanzar hacia la neutralidad. En este análisis habéis aprendido que hace 100 años el hidrógeno electrolítico ya tuvo un recorrido hasta que fue desplazado por el carbón y gas natural, sin embargo, cuando la marea fósil que hemos vivido los últimos 80 años retroceda, este tipo de proyectos industriales volverán a extenderse. Muchas veces pensamos que somos muy disruptivos hoy en día, pero no somos conscientes cuantas cosas “arrasaron” los combustibles fósiles… que, desgraciadamente, tienen un coste económico relativamente bajo, pero tiene un coste medioambiental que no se hacen cargo. Por eso cuesta hoy en día que la descarbonización encaje en la rentabilidades esperadas, porque compite contra algo “dopado” como diría un aficionado al deporte.
ANÁLISIS PREVIOS en “Energy Analysis”:
Muchos sois nuevos lectores por lo que os dejo alguno de los análisis llevados a cabo:
81) Combustión de mezclas de hidrógeno-gas natural aplicada a la cocción de productos cerámicos: emisiones y propiedades de llama
En el boletín número 76 traté la descarbonización de la industria del vidrio, esta vez, desgranaré un estudio técnico realizado por el Instituto de Tecnología Cerámica y Sociedad Española Carburos Metálicos, donde analizan la descarbonización del proceso de secado y cocción de la cerámica gracias al hidrógeno verde.
112) Análisis sobre el mercado europeo de electricidad 2022
Europa, aunque nos guste imaginarnos como el centro del mundo, no dejamos de ser un pequeño apéndice de la placa tectónica euroasiática. En los últimos siglos hemos vivido en una época que bien podría llamarse el eurocentrismo. Este tiene su germen en la primera circunnavegación capitaneada por Juan Sebastián Elkano, considerado por muchos la mayor proe…
104) De electrones a moléculas: Haru Oni
En el análisis de hoy, voy a describir el proyecto Haru Oni, que se esta llevando a cabo en Punta Arenas (Región de Magallanes, Chile), donde se pretende aprovechar la electricidad renovable generada para la obtención de e-fuels. Siempre se dice que las energías renovables no están centralizadas, como ha sido el caso del petróleo. Aunque esto no es ciert…
Muchas gracias Ager. No tenia ninidea de los electrolizadores de los años 20. Muchas gracias. Totalmente de acuerdo, cuando juegas con doping, te acaban pillando, y cuanto mas seamos conscientes, mas facil pillarlo